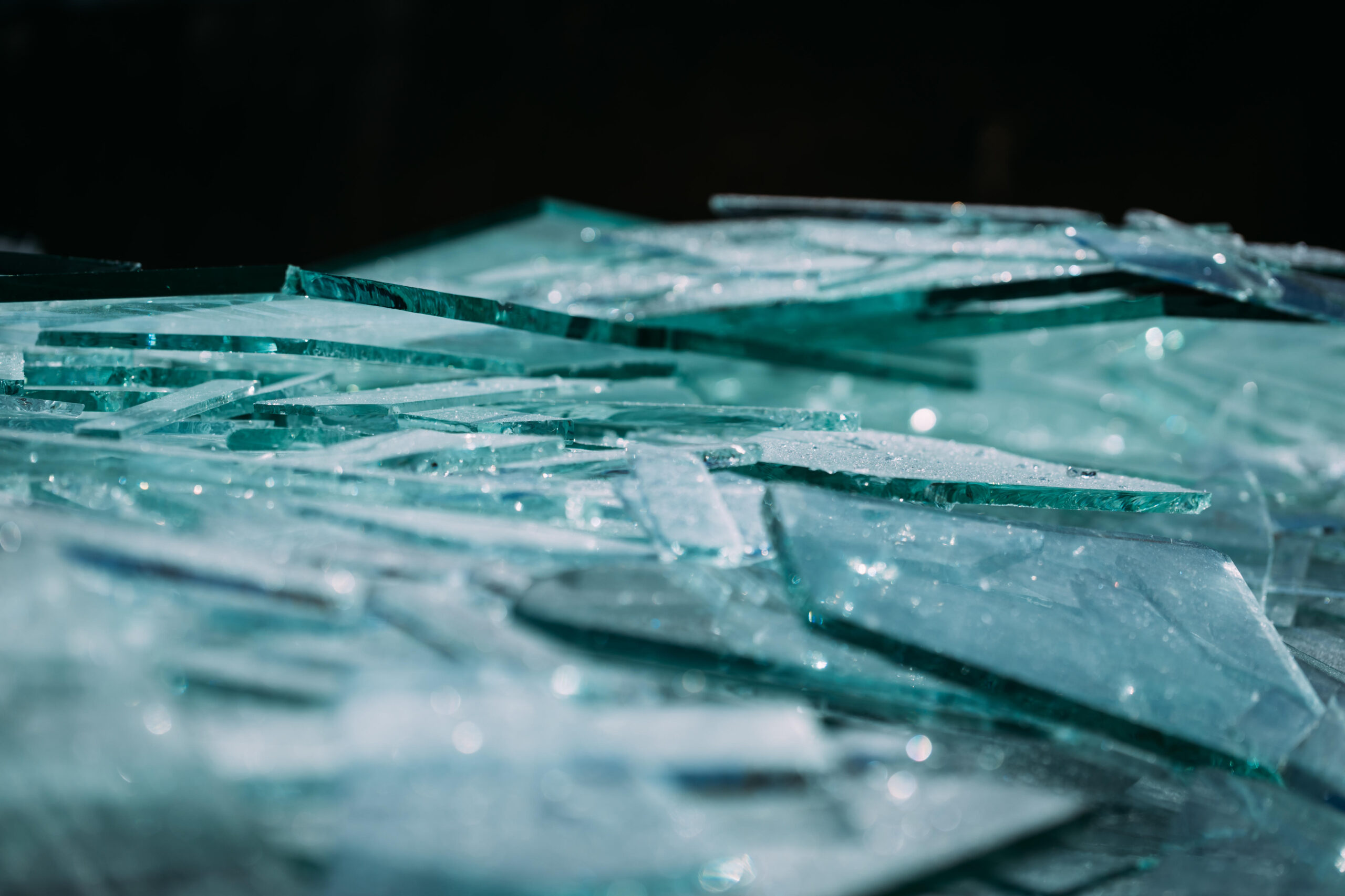
Na drodze do osiągnięcia neutralności klimatycznej Saint-Gobain wprowadziło w ubiegłym roku strategię Grow & Impact, której głównym celem są szeroko zakrojone działania na rzecz walki z ociepleniem klimatu oraz zapewniania komfortu użytkownikom budynków bez obciążania planety. Cel nadrzędny „Making The World a Better Home” przyświeca wszystkim markom należącym do Grupy, a deklaracja czynienia świata lepszym domem zaczyna się już w zakładach produkcyjnych – m.in. od wykorzystania stłuczki szklanej do produkcji szkła budowlanego (przeszkleń fasadowych, okiennych czy szkła do wnętrz) oraz samochodowego.
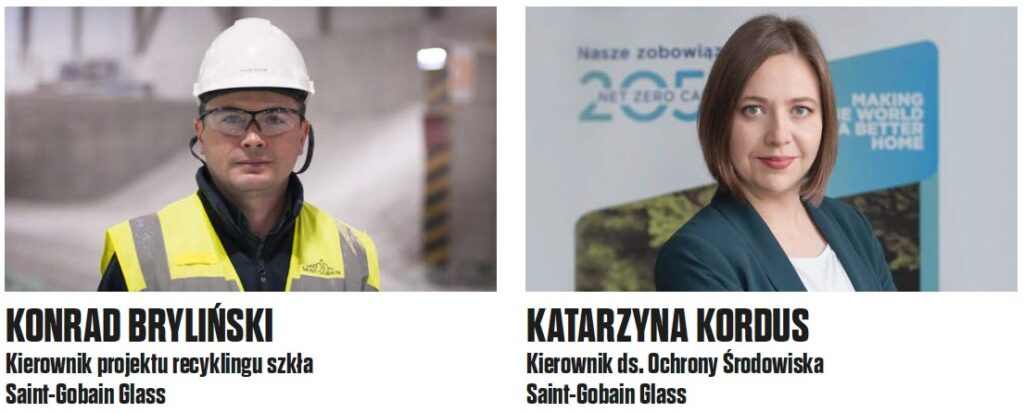
Builder: Gospodarka o obiegu zamkniętym jest przyszłością każdej gałęzi przemysłu. Jakie znaczenie dla procesu wytopu szkła pod kątem technologicznym ma stłuczka szklana?
Konrad Bryliński: Stłuczka sama w sobie jest już szkłem, a więc naszym produktem finalnym. Jedyne, co trzeba z nią zrobić, to – w dużym uproszczeniu – ponownie przetopić i na nowo uformować. W przeciwieństwie do szkła uzyskiwanego z wytopu mieszanki surowców szklarskich, gdzie musi dojść do odpowiednich reakcji i wiązań oraz częściowych strat wynikających z tych cyklów, sam proces ponownego przetopu stłuczki jest dużo prostszy, a co za tym idzie – mniej energochłonny i, co bardzo ważne, prawie bezstratny.
Czyli pod kątem ochrony środowiska dozowanie stłuczki szklanej do procesu produkcji ma pozytywny wpływ na klimat?
Katarzyna Kordus: Jak wspomniał Konrad, recykling stłuczki to proces zdecydowanie mniej energochłonny, ponieważ do jej przetopienia zużywa się nawet 30 proc. mniej energii, niż ma to miejsce w przypadku wytwarzania szkła z surowców naturalnych. Niesie to za sobą wymierne korzyści dla środowiska w postaci znaczącego obniżenia emisji m.in. gazów cieplarnianych przez zakłady. Każda tona stłuczki szklanej to oszczędność ok. 300 kg CO2 z powodu mniejszej ilości spalanego paliwa oraz braku rozkładu surowców węglanowych z uwagi na to, że stłuczka jest już materiałem przetworzonym. Recykling przyczynia się również do zmniejszenia konsumpcji surowców kopalnych, takich jak piasek, wapień czy dolomit, które są zastępowane stłuczką.
K.B.: Dodam jeszcze, że tego typu produkcja jest praktycznie bezstratna – z 1 tony odpadu szklanego uzyskujemy ponownie 1 tonę szkła. Dla porównania: do wyprodukowania 1 tony szkła z surowców pierwotnych potrzebujemy ok. 1200 kg mieszanki szklarskiej, w tym aż 750 kg piasku.
Jakie wymogi odnośnie do jakości surowca musi spełniać stłuczka szklana wykorzystywana do produkcji szkła płaskiego?
K.B.: Wymagania dotyczące stłuczki szklanej dla produkcji szkła płaskiego są bardzo restrykcyjne. Co do zasady – surowiec, który do nas dociera, powinien być pozbawiony Stłuczka szklana w zakładzie Saint-Gobain Glass w Aniche jakichkolwiek zanieczyszczeń. Właściwie powinno to być tylko potłuczone szkło płaskie, w dodatku posegregowane gatunkami/ kolorami. Obecnie w całość stłuczki zewnętrznej zaopatrujemy się za pośrednictwem recyklerów, którzy powinni być gwarantem jakości oferowanego towaru. Polscy dostawcy stłuczki szklanej do produkcji szkła płaskiego pozyskują ją dla linii Float głównie z rynku pre-consumer (zakłady przetwarzające szkło), gdzie ryzyko wystąpienia zanieczyszczeń jest relatywnie niskie. Jakość dostarczanej do nas stłuczki szklanej weryfikujemy, poddając ją kontroli wizualnej w trakcie dostawy oraz podczas załadunków surowca do silosów dziennych, gdzie na taśmociągach zamontowane są silne magnesy stałe oraz detektor metali, co chroni proces produkcyjny przed groźnym w skutkach zanieczyszczeniem metalami. W przyszłości, kiedy będziemy pozyskiwać i przetwarzać szkło z rynku post-consumer, a więc z rozbiórek czy renowacji budynków, ryzyko występowania zanieczyszczeń będzie na pewno wyższe, chociażby związane z obecnością innych odpadów remontowych, np. gruzu. W takim przypadku niezbędna będzie rozbudowa systemu detekcji o detektory optyczne, pozwalające na wychwycenie tego typu zanieczyszczeń, jak wspomniane kamienie czy też ceramika lub porcelana, które w skutkach są równie niebezpieczne jak zanieczyszczenia metalowe. Pierwsze linie tego typu, przeznaczone do weryfikacji jakości oraz doczyszczania stłuczki z rynku post-consumer, powstały już w naszej Grupie w zakładach we Francji oraz w Rumunii.
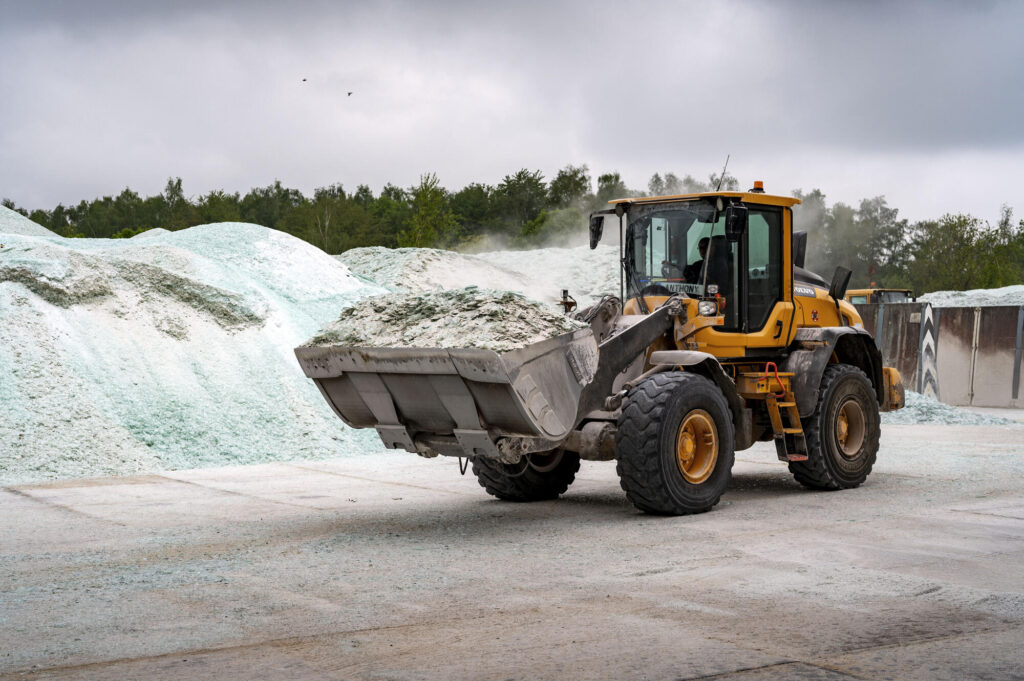
Produkcja zgodna z GOZ i recykling stłuczki szklanej to jeden z ważniejszych kroków Saint-Gobain na drodze do osiągnięcia neutralności klimatycznej. Jak przedstawia się strategia zwiększania zużycia stłuczki opracowana przez Grupę?
K.K.: Cele zostały sprecyzowane bardzo jasno: średni udział stłuczki w wytopie dla linii Float w zakładach Saint-Gobain powinien sięgać co najmniej 50 proc. do 2050 roku, 25 proc. surowca ma pochodzić z rynku pre-consumer (stłuczka pochodząca od przetwórców szkła), 10 proc. z rynku post-consumer (stłuczka poużytkowa), zaś pozostały odsetek stanowić będzie stłuczka własna (generowana na miejscu w zakładzie). W naszej strategii wyznaczyliśmy również cel pośredni na 2030 rok, jakim jest wykorzystanie stłuczki szklanej do produkcji szkła na poziomie 40 proc., w tym 20 proc. surowca z rynku pre-consumer i 5 proc. z rynku post-consumer.
K.B.: Aby osiągnąć te cele, będziemy kontynuować naszą politykę współpracy z recyklerami na rynku lokalnym, starając się pozyskiwać od nich jak największe ilości stłuczki wysokiej jakości. Dużo trudniejszym wyzwaniem, które z pewnością zdeterminuje nasze działania w najbliższym czasie, będzie skupienie się na rynku post-consumer, który w Polsce dopiero raczkuje. Prognozy i analizy dotyczące dostępnych wolumenów w perspektywie kilku lat są bardzo optymistyczne.
Biorąc pod uwagę udoskonalanie technologii wytwórczych, jak przedstawia się przyszłość procesu wytopu szkła w duchu low-waste w zakładach Saint-Gobain?
K.K.: W obliczu wyzwań środowiskowych, z jakimi przychodzi się mierzyć producentom i konsumentom, świat zmienia się bardzo dynamicznie. Jesteśmy świadkami ogromnego postępu technologicznego, dlatego z założenia nie możemy wykluczyć powstania zupełnie nowej technologii produkcji szkła płaskiego, która zdominuje rynek – podobnie jak miało to miejsce z technologią Float, wynalezioną w latach 50. ubiegłego wieku. W perspektywie kilku najbliższych lat, opierając się na obecnych metodach produkcyjnych i przy konsekwentnej realizacji założeń strategii Saint-Gobain Grow & Impact, nasze główne działania skupiać się będą na maksymalizacji udziału stłuczki oraz pozyskiwaniu energii wykorzystywanej w całym procesie wytwórczym z OZE. Podjęliśmy już pierwsze kroki w tym kierunku, m.in. podpisując długoterminową umowę na pozyskanie energii elektrycznej z farm wiatrowych od firmy Tion Renewables AG czy też uruchamiając na skalę przemysłową produkcję szkła bazowego ORAÉ, które dzięki wykorzystaniu 70 proc. stłuczki i energii pochodzącej w całości ze źródeł odnawialnych – łącznie z biometanem wykorzystywanym do wytopu – jest produktem o zredukowanym śladzie węglowym. Do tych osiągnięć należy dodać również pierwszą na świecie bezemisyjną kampanię produkcyjną szkła tzw. zero carbon, która miała miejsce w maju tego roku w Saint-Gobain Glass w Aniche we Francji. O sukcesie zadecydowało właśnie wykorzystanie 100 proc. stłuczki szklanej, 100 proc. zielonej energii produkowanej z biogazu oraz zdekarbonizowanej energii elektrycznej.
K.B.: W perspektywie średnioterminowej z kolei będziemy mieli z pewnością do czynienia z hybrydyzacją pieców i wanien szklarskich. W nowych typach znacząco wzrośnie udział energii elektrycznej w procesie wytopu szkła – będzie to jednak energia pochodząca w dużej mierze z OZE. Choć obecnie trudno wyobrazić sobie całkowite wyeliminowanie gazu w procesie produkcyjnym, z pewnością w przyszłości będzie go można zastąpić innym ekogazem lub wodorem. Nasze zespoły R&D już pracują nad koncepcją nowoczesnych, „zielonych” pieców i mamy nadzieję, że wkrótce tego typu innowacje zagoszczą w hucie szkła w Dąbrowie Górniczej. Nasze ostatnie inwestycje i sukcesy odnoszone na polu zrównoważonej produkcji pokazały, że jesteśmy na dobrej drodze do dekarbonizacji naszych zakładów dla dobra planety i ludzi.